What is Petroleum Vapor Intrusion?
By Jeremy S. Kinman, LPG, PG
Vapor intrusion (VI) is the general term given to the migration of volatile organic chemicals (VOCs) from any subsurface contaminant source, such as contaminated soil or groundwater, through the air-filled pores of unsaturated soils (vadose zone) and into an overlying building. In extreme cases, these vapors may accumulate at concentrations causing near-term safety hazards (e.g., explosions or acute health effects) or aesthetic problems (i.e., nuisance odors). There are two classes of VOCs that account for the majority of sites with contaminated soil and groundwater:
• Chlorinated solvents used in the dry-cleaning industry, industrial settings for degreasing, manufacturing or other purposes.
• Petroleum hydrocarbons (PHCs) released from underground storage tanks (USTs) like those that exist at your neighborhood convenience store, aboveground storage tanks (ASTs) at bulk fuel facilities, or fuel-delivery tanker/pipeline catastrophic incidents.
Chlorinated solvents and PHC-related VOCs exhibit unique chemical properties that affects their subsurface transport. These differences mandate distinct screening procedures specific to each group. Here we will further explore the potential sources and screening process associated with petroleum vapor intrusion (PVI).
What Are the Causes of Petroleum Vapor Intrusion?
Practical field experience and published literature of field studies show that PVI impacts are generally associated with:
1. Direct contact of LNAPL, or very high dissolved concentrations, to a building foundation;
2. Close proximity of LNAPL, or very high dissolved concentrations, to a building foundation in direct contact with fluctuating groundwater that is contaminated;
3. Direct contact of LNAPL, or very high dissolved concentrations, to building sumps or elevator shafts; and,
4. Direct contact of LNAPL, or very high dissolved concentrations, with a preferential pathway (e.g., improperly-sealed utility lines).
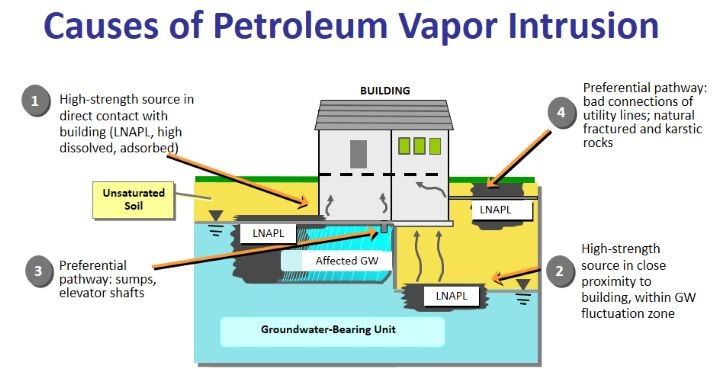
Adapted from Ririe, 2009
What Does the Guidance Tell Us About PVI?
In the past decade, there has been a significant increase in attention to VI issues and several recent regulatory guidance documents have been developed by State and Federal agencies for assessment and management of PVI. Much of the recent PVI guidance, including the Indiana Department of Environmental Management (IDEM) Remediation Closure Guide (RCG), presents guidance as a series of steps in a screening process.
• Step 1: Can the site be categorically excluded from sampling, or “screened out”? Preliminary criteria that can eliminate sites from further vapor intrusion assessment have fundamentally changed the process for investigating the VI pathway.
- Based on soil and groundwater concentrations and depth/distance to source.
- For Indiana properties, IDEM will not request evaluation of the VI exposure pathway at an in-use (active) UST facility (source: IDEM “Vapor Intrusion Investigations at In-Use Underground Storage Tank Facilities,” August 2014).
• Step 2: Can preliminary “screen out data” be collected?
• Step 3: Perform PVI assessment if necessary.
Preliminary PVI Screening Criteria:
In Indiana, a property screens out from the PVI pathway if:
• No emergency conditions are present (petroleum vapors);
• No significant preferential pathways are present;
• No free product is present within 30 feet, horizontally or vertically, of the building foundation;
• Groundwater benzene concentrations are ≤1,000 micrograms per liter (µg/L) within 5 feet of the building;
• Groundwater exceeding RCG vapor intrusion groundwater screening levels (VIGWSLs) is not in direct contact with building; and,
• > 5 feet of clean, unsaturated soil with oxygen levels measured at > 5% separates the building from residual petroleum.
The Interstate Technology Regulatory Council PVI Guidance Document contains regulatory contact information and guidance for states other than Indiana.
What If My Property Doesn’t Screen Out?
The fundamental difference between PVI and VI resulting from chlorinated compounds is biodegradation. Unlike vapor intrusion associated with chlorinated compounds, vapors from petroleum hydrocarbons rapidly biodegrade as they migrate through unsaturated soils greatly limiting the potential for the PVI pathway to be complete. Because of the rapid biodegradation of petroleum vapors, compared to the slower degradation of chlorinated compound vapors in the subsurface, the number of sites with a completed PVI pathway is significantly fewer than those contaminated with chlorinated compounds. However, PHC vapors can migrate into buildings under some circumstances. For example, PVI would more likely occur in a building located above shallow contaminated soil, such as the area near a UST, or in instances where a building footprint or asphalt parking area is large enough to limit the movement of oxygen beneath it.
The first step to determine if your building may be affected by PVI is to collect basic data to develop a Conceptual Site Model (CSM). In general, a CSM is a comprehensive description of the site, contaminant distribution, and processes by which the contaminant migrates to receptors. The following details will serve as the basis for any initial CSM:
• Property use (residential, commercial, industrial);
• Building construction type (slab, crawl-space, basement);
• Vadose zone characteristics (soil type, moisture content, porosity, etc.);
• Type and age of the contamination (diesel vs. gasoline);
• Source strength;
• Depth of the source (vertical distance from source to building); and,
• Lateral distance between the source and the building.
If the evaluation and analysis of the CSM suggests the building may be potentially affected by PVI, a focused vapor investigation should proceed as follows:
• Conduct a building survey to determine potential background sources (many commonly used household products contain some of the target compounds of concern and may confound results);
• Collect indoor air data;
• Collect sub-slab or exterior soil gas data; and,
• Evaluate data against applicable screening levels.
Federal and state-level regulatory agencies have issued specific guidance for evaluating if your building may be potentially affected by PVI. In most instances, the building will screen out from PVI, while additional evaluation and data collection is necessary for others. Every site brings its own unique challenges and Wilcox Environmental Engineering is ready to help you solve your environmental problems. If you have any questions, or would like to discuss further, please call Jeremy Kinman, LPG, PG at 1-877-683-8378 or email at jkinman@wilcoxenv.com.